Industrial Research Fellow
"We can only achieve this if industry and research work closely together“
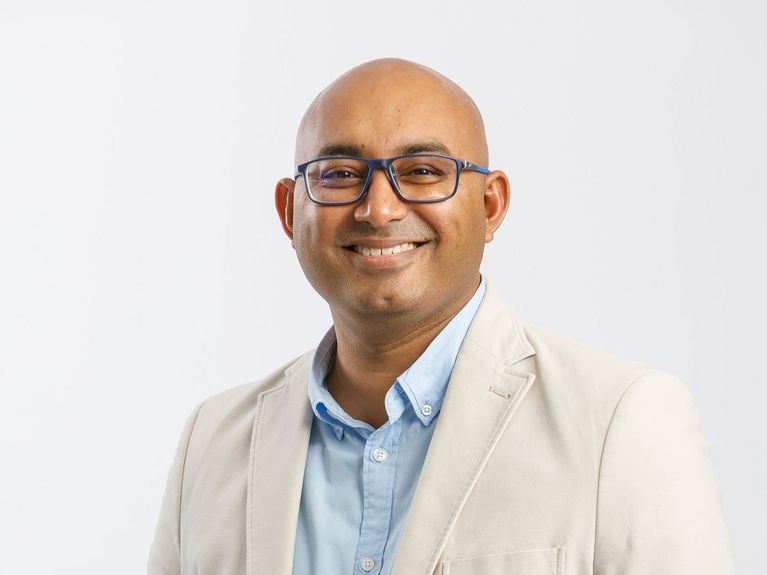
Dr. Denzil Moodley will contribute his expertise at HZB with the aim of accelerating the innovation cycle for sustainable fuel technologies in aviation. Picture: Sasol
Helmholtz-Zentrum Berlin is breaking new ground in its cooperation with industry. An industrial research fellowship brings a chemist from the South African company Sasol on board, who is playing a leading role in the development of catalysts for sustainable aviation fuel.
Denzil Moodley likes to have a tried-and-true attraction for visitors: he shows them a few drops of liquid, one of the results of his research to date. He works for the South African chemical giant Sasol, which, together with the Helmholtz-Zentrum Berlin (HZB), the Karlsruhe Institute of Technology (KIT) and other partners from industry and science, is developing new catalysts for the production of a climate-neutral aviation fuel. Moodley holds up a container: "It's always nice to be able to show off this little bottle of kerosene made from our new catalyst!"
The goal is ambitious: enable a process that can be used to produce aviation fuel on a large scale from the feedstocks CO2 and green hydrogen. The seven project partners from Germany and South Africa want to develop catalysts for a crucial step in this process, the Fischer-Tropsch synthesis. These catalysts are essential for the large-scale production of green kerosene: the more sophisticated the catalysts, the more efficiently so-called Sustainable Aviation Fuels (SAF) can be produced. In the Fischer-Tropsch process, which has been known for decades, carbon dioxide is used to produce a synthesis gas that can be used, for example, to produce synthetic fuels. This process requires a lot of energy, but its efficiency and jet-fuel yields can be significantly improved with an optimized catalyst. This is the goal of the South African-German innovation project CARE-O-SENE supported by the Federal Ministry for Education and Research (BMBF).
Denzil Moodley plays a key role. He and his research group are responsible for scaling up the process to a semi-industrial scale - from a small bottle of fuel to thousands of liters. "We can only do this if industry and research work closely together," says Denzil Moodley, "everyone has their own methods and strengths, which we combine in our project. As an Industrial Research Fellow, he is now taking a closer look behind the scenes at HZB and contributing the industrial perspective. "Normally, you work on your own topics and then have a few interactions with the project partners," says Denzil Moodley. "The fellowship now allows us to propel the relationships we have built to the next level. We are having more conversations, more interaction, more joint planning."
"As a first step, we have identified four different catalysts - some that are in an advanced developmental phase, and others that promise even greater efficiency but need to be further developed," explains Denzil Moodley. The South African company he works for, Sasol, has decades of experience with Fischer-Tropsch technology and a well-positioned catalyst development department - but the link with HZB opens up new possibilities: "We don't have access to a synchrotron in South Africa," says Moodley. "Normally, we use a catalyst, let the reaction run and then analyze the catalyst (post-mortem). But thanks to HZB, we can observe it directly during the reaction." This gives the researchers a much better idea of where things can be optimized.
Sasol Sasolburg site, with the 60m high, 300 barrel/day FTDR ( Fischer-Tropsch Design Reactor) in the foreground. The FTDR was used for semi-commercial testing of one of the scaled-up CARE-O-SENE catalysts. Picture: Sansol
One of the special features of CARE-O-SENE is the speed at which research is carried out: while one working group is characterizing potential catalysts, another is already starting to evaluate the substances from a technological and economic point of view. And still other researchers are considering how to process the catalysts after use (regeneration), since the materials used are expensive. All these aspects fit together like a giant jigsaw puzzle. Denzil Moodley's piece of the puzzle is scaling - how can a catalyst be produced and used on a large scale? The question is far from trivial: "If you look at the catalyst under a microscope, you will see that the active particles are tiny, we are talking about six to ten nanometers," he says. "When you work with small quantities of catalysts in glass equipment in a lab, it is completely different from industrial scale where the preparation equipment is much larger, making tonnes of material, and the Fischer Tropsch reactors themselves 20 or even 50 meters high. So how do these tiny particles behave in a very different hydrodynamic environment where you have tons of material reacting, and where the gas profiles alone are completely different?"
The rapid pace of innovation in the CARE-O-SENE project is a key advantage, because the demand for climate-neutral kerosene is enormous - and the issue is becoming more relevant as the number of air passengers continues to grow. On the other hand, the pace is challenging for the researchers involved, and close coordination across continents is becoming a key criterion for success.
This is where the fellowship comes in, bringing Denzil Moodley and HZB closer together. The aim of the investigators is to gain a better understanding of the work of the partners involved and to develop new ideas together through close exchange. The high expectations of this novel fellowship program are clear from the statements of the partners involved: "This is a confirmation of our commitment to promote effective partnerships that bridge the gap between research and industry," says Bernd Rech, scientific director of HZB. And Theo Mudzunga, Sasol's Vice President of Research and Technology, emphasizes: "Partnerships between industry and research are essential to drive innovation at the pace and scale needed to address global challenges.
Denzil Moodley has now tried out what this mutual learning looks like on a day-to-day basis. He particularly appreciates having more time to engage in the discussions and the intricacies of his colleagues' work in Berlin. And the exchange with the doctoral and postdoctoral students at the HZB has proven to be valuable. "For example, if one of them is doing an experiment with a certain model catalyst, we discuss how close the experiment is to the realistic conditions that will later have to be met in production," explains Denzil Moodley. The young scientists have a clearly defined area of responsibility in the project - and he can help them see the bigger picture and understand where their task plays an important role in the overall project.
Denzil Moodley believes the fellowship program could well continue. He has already seen interest from colleagues at his company: "Now that we have a positive experience on both sides," he says, "there’s certainly possibilities to extend it to other researchers and other projects"
Leading Sasol scientist appointed as Industrial Research Fellow at HZB
Readers comments