Sustainable flying
Making a clean takeoff with electric engines
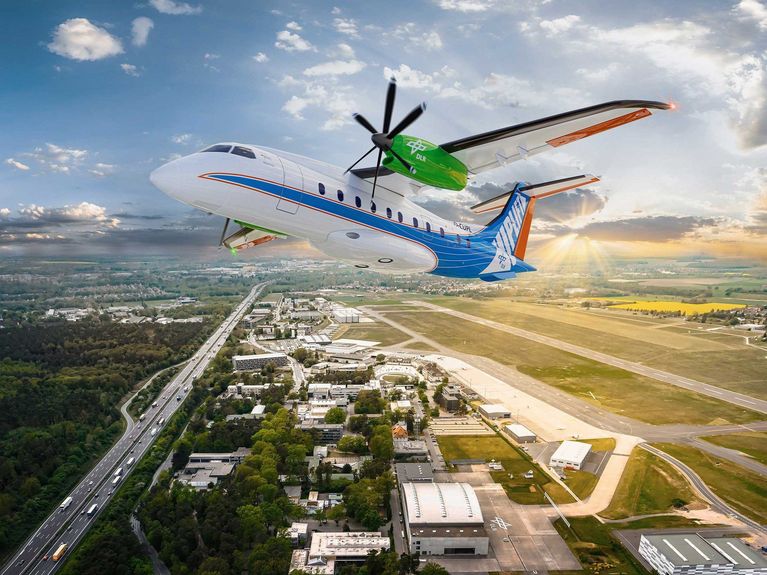
The Dornier 328 UpLift will be used as a flying testbed for climate-friendly aviation technologies, such as fully synthetic fuels or hydrogen as a potential sustainable future aircraft fuel. Credit: DLR (CC BY-NC-ND 3.0)
“Civil aviation is currently responsible for three percent of total CO₂ emissions worldwide. And that figure is growing steadily, by around five percent a year,” says Lars Enghardt. “In other words, the number of active aircraft doubles every 20 years or so.” If these planes continue to fly on fossil kerosene in the future, the climate targets will never be met. That’s why the DLR founded the Institute of Electrified Aero Engines, which the physicist heads, in Cottbus in June 2020. “Our goal is to make aviation climate-friendlier, and ideally even climate-neutral,” says the Professor of Electrified Aircraft Propulsion Systems. “To that end, we are now creating a DLR institute with a completely new research infrastructure in Cottbus.”
Lars Enghardt, Director of the DLR Institute of Electrified Aircraft Engines in Cottbus. Picture: Kai Dürfeld
This is where future aircraft propulsion concepts will be developed. The DLR is pursuing research on a wide range of variants – from classic gas turbines powered by synthetic, climate-neutral fuels, to hybrid electric systems and alternative propulsion systems based on batteries or hydrogen. With a focus on the last two topics, the DLR purchased a 13,500-square-meter warehouse on a former military airfield in Cottbus. Over the next few years, a test landscape will be created there, where the institute will work with partners from industry to test the aircraft engines of tomorrow.
One of these concepts that Enghardt and his team have already driven forward is called H2Electra. “We want to show what the purely electrically powered regional aircraft of tomorrow could look like,” he says, pointing to the model, which is roughly one-tenth scale and features a Plexiglas fuselage that reveals its inner workings. “We thought about what the inside of a plane with electric motors might look like,” he continues. “This helps us to understand where we need to revisit previous aircraft concepts based on gas turbines.”
The H₂Electra model shows the possibilities of operating an electric regional aircraft, fueled with hydrogen. Picture: DLR (CC BY-NC-ND 3.0)
In terms of aerodynamics and design, they largely looked to established models on today’s regional aircraft market. But that’s where the similarities end. The new concept doesn’t rely on fossil kerosene, but on hydrogen produced from renewable sources. And that requires making far-reaching changes. “Gaseous hydrogen takes up an incredible amount of space, which would seriously limit range,” says Enghardt. “We either have to significantly compress it or liquefy it at extremely low temperatures.” Though neither process is anything new, both require an extremely thick-walled fuel tank. And that doesn’t fit in with current aircraft concepts. “Today, fuel is stored in the wings, both in the main wings and at the rear, in the horizontal stabilizers,” the physicist explains. Since there’s no need for pressure tanks, the wings can be very flexible. And this is important, as the aerodynamics are precisely tailored to this. And they’re what ensures that an aircraft flies efficiently in the first place. “You can’t feasibly achieve the same wing flexibility with a hydrogen tank,” he explains. “That’s why it has to be located in the fuselage, which creates certain space problems compared to current interior designs.”
There are also various options for how the hydrogen then provides electrical energy for propulsion. On the one hand, it could be burned in a gas turbine to drive a generator. Or it could be converted directly into electricity in a fuel cell. In the H2Electra, the electricity in turn drives as many as six electric motors that can be attached to the wings of the concept aircraft. “To help us analyze the various approaches as comprehensively as possible, our test aircraft has a modular structure,” says the physicist. But at the end of the day, it is and remains a prototype that will probably never actually fly.
Putting tomorrow’s technologies to the test
But that’s not true for UpLift – another project in which the Cottbus-based institute is involved. “The goal of the UpLift project is to drive forward climate-friendly aviation, particularly in Germany,” says Enghardt. “Accordingly, we’re working to accelerate the development and market launch of products for our industrial partners.” The “turbochargers” for that purpose are ground-based test benches, which are used to prepare the aircraft components for subsequent flight tests. Over the next few years, these will be constructed at the more than 20 DLR institutes involved in the project throughout Germany and then be used by UpLift’s industrial partners to test the newly developed aircraft components. “UpLift was launched by the Federal Ministry for Economic Affairs and Climate Action and is coordinated and supported by the Project Management Agency for Aviation Research,” he explains. “The DLR has taken on a key role here, as it will construct and operate all the test benches.”
In the end, there will be just under 30 test benches, including three in Cottbus. Two of those will deal specifically with fan technology, which is absolutely vital for electrically powered aircraft. Why? Because both fuel cells and batteries don’t just produce electricity; they also get hot. And that can be a problem. “With a classic gas turbine, the heat is automatically transported outside via the exhaust gas jet,” Enghardt explains. “With batteries and fuel cells, you have to actively dissipate the heat. Otherwise the system overheats and breaks down.” The first test bench will therefore be used to develop concepts for new types of heat exchangers and to examine the individual elements in the model. Once this step has been completed, the second test bench in Cottbus will be used to stress-test future active ventilation systems. And the third test bench will do the same, but for complete drive trains: “It’s a full-system test bench for fuel-cell-based drive concepts and a joint project with the company MTU,” says Enghardt. “MTU is currently building it in Munich. It will be handed over to us in Cottbus in 2030, after which we’ll operate it there.”
Forschungsflugzeug D328 UpLift - „Flying Testbed“ für neue Wasserstoff-Technologien
And will the new technologies also be tested in the air? “That’s a second important pillar of the UpLift project,” he explains. “The DLR has already purchased an aircraft for this purpose – a Dornier 328 that we can use as a research platform.” Currently, the interior of the aircraft is still virtually empty, so that it can be individually equipped with specific measuring instruments or experiments for various testing purposes. Further, its design is so flexible that it can be converted and expanded for various propulsion systems based on fuel cells, batteries or even direct hydrogen combustion. “This allows us to take the promising concepts that we have evaluated on the test bench, approved, and developed further as part of collaborative research units, and actually demonstrate them in flight tests.”
Readers comments